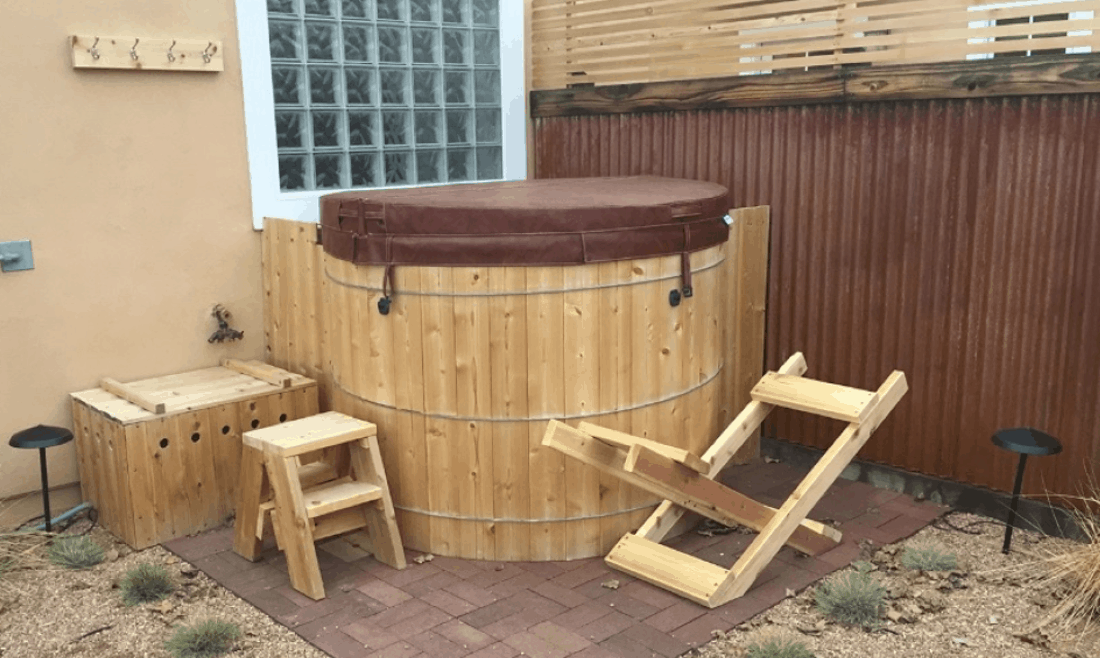
I always wanted to build a cedar hot tub. The vision of a long soak in a hot tub under the starry skies on a clear, crisp night in Santa Fe is quite compelling. Doing it in a natural tub constructed from cedar made the thought seem even better.
As an experienced DIYer, I was taken by the idea that I could design and build a classic, red cedar hot tub myself. And I could save several thousand dollars over the cost of a kit from an established hot tub supplier. After all, how hard could it be? I built my own home in 2014. A cedar hot tub is a far simpler and much smaller project.
This is the basic hot tub I envisioned:
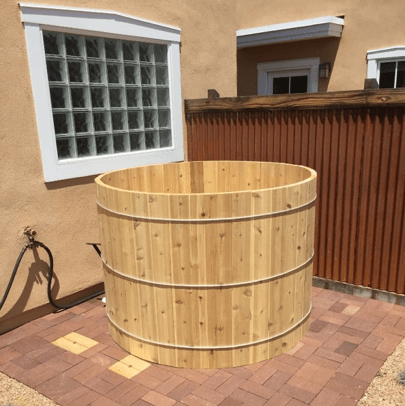
Research
I spent several weeks scouring websites of commercial suppliers and DIY builders for ideas about wooden hot tubs. In my search, I discovered three things:
- I confirmed my preference for a circular, cedar tub. Done well, they really look nice. And “natural” is good, right? No plastic spa for this guy!
- Kits were priced from $6,500-8,000 for a five-foot-diameter tub. They looked great but were definitely out of our budget. A bit of back-of-the-envelope scribbling convinced me I could do it for well under $3,000. That included a complete spa pack (electric heater, pump and filtration system).
- A couple DIY builds that I researched revealed some issues that I was certain my design would avoid. I had convinced myself that a cedar hot tub was just a big barrel, and big barrels have been built for centuries. After all, the first wooden hot tubs popularized in the 1970s were often discarded redwood wine-making barrel sawed in half. Easy-peasy, right?
How to Build a Cedar Hot Tub: The Design
After my research was finished, I began the design phase. The tub would be circular, five feet in diameter and about 40 inches deep. I would use 2×6″ STK (select tight knot) red cedar from Home Depot, carefully picking through stacks of lumber to get the clearest, straightest pieces I could find.
This material choice kept the project within the target budget. It wouldn’t have the same aesthetics of commercial tubs built with the best clear red cedar. However, having a few knots was worth the $2,000-2,500 savings in wood alone. If I lived closer to cedar forests and mills, the cost differential might not have been as significant. Clear cedar is very striking wood—but it’s expensive.
The basic design in place, I needed to decide on a joinery strategy. There were only three serious options. But they all started from the baseline that each stave (the vertical pieces in a barrel) needed to be trimmed at an angle so when they were placed they would form a circular pattern. That way, all the facing surfaces would be flush. The math is easy since you begin with 360 degrees divided by the number of staves. In my case, this was 40 staves giving 9 degrees per stave. This would require each side to be trimmed to 4.5 degrees on the table saw.
Designing the Joints
The joint details are a bit more complicated, since the tub needed to watertight. A flat, surface-to-surface joint seemed the easiest since no additional cutting would be necessary after the initial trimming. Wine and whiskey aging barrels are constructed with this joint. That said, I wasn’t certain I could cut the joints accurately enough with the lightweight, jobsite table saw I would be using.
That left me with either a spline joint (a groove cut in each face with a separate spline that fit into the grooves) or a cove-and-bead joint (also called a canoe joint). The former could be cut with my table saw. But I was concerned with accuracy since the spline was relatively thin and really called for a cabinetmaking-quality saw. The cove-and-bead joint offered more surface area to seal the joint and I was convinced all I needed was a couple of bits and a router table. A chance to buy another tool should never be passed up. So, I decided on the canoe joint which is shown in two pictures below. (Scroll down to see the photos of the staves.)
My final design decision was to determine how to clamp the staves together. Barrel makers use fixed diameter metal hoops which are driven down over the tapered staves. Commercial cedar hot tub makers typically use adjustable stainless-steel bands. While I liked the appearance of these bands, sourcing options were limited, expensive and required providing tight dimensions when purchased. I decided that vinyl-coated galvanized steel wire rope was the best option. It was inexpensive, could be sized in the field during assembly and was easily sourced.
Note to Readers Who are Serious Tech Geeks:
I used Fusion 360 to do the layout and dimensioning for the stave and tub bottom design. You can do the same calculations with pencil and paper. It was a fun exercise which also made me appreciate the value of top-notch (and free for the DIYer) CAD tools.
Build a Cedar Hot Tub: Preparing the Platform
A full, five-foot diameter, 40-inch deep hot tub holds almost 400 gallons of water. This is over 3,300 pounds. Yes, that’s 1.65 tons. Add the weight of the water-soaked wood and you can easily approach two tons. Do NOT under any circumstances build this tub on a wooden deck elevated any distance unless you are absolutely certain the structure can hold the weight. I can’t stress this enough. The risk of a collapsing deck with two tons of water is very real and very dangerous. You could die.
Another caveat, albeit with much less risk to life and limb, is to avoid building your tub directly on the ground without any site preparation. Remember, we are dealing with two tons distributed over a relatively small surface area. The possibility of the tub tipping if the ground gets heavily soaked is very real. It may not tip all the way over but sitting in tub even 10 degrees off vertical is uncomfortable and looks quite like an amateur build.
That’s why you should use either a concrete pad (existing or new) or a properly built platform that will be stable under the weight of a full tub. For my project, I decided to build a new platform using brick pavers.
The completed brick platform is shown above. Not visible is the four inches of compacted base course gravel covered with at least an inch of sand. You must compact the base course. A hand tamper works fine if you build up the gravel up an inch at a time and don’t skimp on the tamping. Do the same with the sand by tamping it into the base course gravel. Once the base is ready and the sand is leveled with a screed, set the bricks with paver edging from your local “big box” store to eliminate the shifting of the edge bricks.
How to Build a Cedar Hot Tub: Materials
Acquiring the materials for this project is straightforward, especially if you live in a larger metropolitan area. For the rest of us, online shopping is a great way to find items that can’t be purchased locally.
Wood
Procuring the wood was the biggest challenge for me. My spreadsheet and CAD calculations resulted in a requirement for 40 44” staves in addition to material for the tub bottom, the bench, a tub cover and a box for the spa pack. The staves and the bottom were to be cut from 2×6” STK cedar. The cover and box would be constructed using 1×6” T&G cedar. At almost $20 for an eight-foot length, the 2×6 material necessitated careful picking through the stack at Home Depot to get the 28 decent pieces I needed.
Alas, I quickly discovered our local Home Depot had only a handful of usable pieces. It took stops at three other stores, all over 60 miles away, before I was able to buy all the 2×6 material for the tub. The tub cover and spa pack box 1×6 T&G material had to be ordered online from Home Depot.
Spa Pack
The hardier homesteader might opt for a wood-fired heater and frequent replacement of tub water to keep the water clean. There are few builds available online, for folks interested in that approach. I prefer my creature comforts delivered with the flip of a switch, so I opted for a pre-configured spa pack with a filter and ionizer unit.
When I built my house, I pre-wired a separate 220V 50-amp circuit off the master bedroom so I could use a 5.5 kw spa pack for faster heating. Using a bromine-based sanitation system and a filter keeps water replacement to every three months, an important consideration in a desert climate where water is a scarce resource.
A Google search for “spa packs” turns up several online vendors. It takes a bit of time and effort to select and configure a spa pack, but it is relatively straightforward once you understand the vernacular of the spa business. I used spaguts.com for my system since their online ordering system was easy to use. They also offer good support for telephone orders.
Clamping System
As I noted above, I planned to use coated wire rope to clamp the staves together. For a five-foot diameter tub, I used three loops of ¼” wire rope, which is sufficiently strong to contain the pressure from the water load.
I made an attempt to purchase the rope, turnbuckles, thimbles and clips locally. But I finally turned to E-Rigging.com for my needs. They have a good “How To” section on using their products. The only downside was the minimum size reel for the wire rope is 200 feet. I have no idea how I will use the remaining 150 feet, but it now sits with the other project surplus items on the shelf in my garage.
IMPORTANT TIP:
You must remove the coating from the wire rope where it wraps around the thimble and is clamped with the clips. Failure to do so may result in a fitting that slips open and, of course, an empty tub.
Tools Needed to Build a Cedar Hot Tub
The major power tools to build this tub are often found in the shops of experienced DIYers. If not, budget about $1,000-1,200 for basic, jobsite versions of these tools:
- Table saw (10”)
- Miter Saw (10”)
- Router table
- A Router (1/2” collet, 2 HP)
- Router bits (1/2” shank, cove and bead)
The list above is linked to the products on Amazon. Home Garden and Homestead receives a small commission from qualifying sales. Thank you!
If you already have heavy-duty, cabinetmaking-quality tools, you will find milling the staves a much easier process. The tools listed here are the bare minimum which requires different techniques to ensure proper milling.
How to Build a Cedar Hot Tub: Construction
OK, we have our platform for the hot tub, purchased our materials, cleaned out the shop and set up our tools. It’s time to make some sawdust!
Tub Staves
I chose to get this task out of the way first, since I suspected it was going to be tedious. It was. First, I cut 20 sticks of 8-foot-long 2×6 cedar in half. (I left them over-sized and trimmed them to 44” after milling). Then, I started cutting the edge bevel on each side of the stave. This went relatively quickly for the 40 staves. The tricky part was cutting the coves and beads. I first needed to set up shims on the top of the router table to adjust the 4.5-degree edge cut to vertical since the router bit is perpendicular to the table surface. Once that was done, I could feed the staves through for consistent cuts. Then things got messy.
I was using a 2.25 HP Bosch router mounted on a decent Bosh router table. Unfortunately, I quickly discovered that my equipment was no match for the depth of cut I needed to make (1/2” for the bead and cove). Not only was it difficult to get a clean cut trying to take it all on one pass, it was decidedly unsafe. REALLY unsafe. Don’t try it.
After an hour or two of testing different cut depths, I finally came to something that worked safely and cut reasonably well. I would need to do four passes for each cove and bead cut. A little arithmetic and I realized that each stave would need to be handled 14 times—twice to cut the edge bevel, four times for each cove and bead milling, twice to cut it to final length with clean cross cuts and twice through the dado blade to cut the groove for the tub floor. That meant handling the staves a total of 560 times. I actually cut four extra staves (and was glad I did) as spares. That brought the stave handling total to 616.
The only way to make this work was to set up a milling process during which I ran all 40 pieces through each cut or depth change (1/8” for the cove and bead) before setting up for the next cut. After more than 8-10 hours over two days, I had the stack of staves as shown below. While the results seemed good enough, it was clear they were not perfect because of all the handling for multi-depth cuts. We would find out later whether they were good enough once we started filling the tub.
The dado is cut to the thickness of the bottom planks. This is typically 1-1/2” – but measure your planks to ensure a tight fit. You must also ensure the distance from the bottom of the dado cut to the end of the stave is the same as the height of the nominal 6” side of the 4×6″ base support on which the tub bottom rests. (The base support should be placed with the 4” side on the platform). This is usually 5-1/2” but purchase and measure your support material first. The goal is to have the weight of the tub bottom resting on base support while also ensuring the stave is flush with the ground to keep out nesting animals.
The Cedar Hot Tub Bottom
In addition to cutting the staves, the 13 boards for the tub bottom also needed cove and bead cut—as well as being trimmed to length. This required another 130 piece handlings in the assembly line process. As the image below shows, I clamped and glued the tub bottom with temporary strips of wood to keep it stable during handling.
I flipped the tub bottom over, drew the appropriate diameter circle and cut it to size with a small saber saw. After moving the bottom outside to the tub location, I cut and screwed two-inch thick foam pieces to the underside. (I used 2-1/2” screws to avoid penetrating the tub bottom). The spaces between the foam pieces are for the 4×6″ pressure-treated lumber base supports on which the bottom rests. Note the tub drain is placed before flipping the tub bottom.
Assembly of the Hot Tub
Once the tub bottom was flipped over and sitting on the supports (not visible in the photo), I began placing the staves around the base. I used temporary screws at the dado cut to hold the first few staves in a vertical position. Fortunately, the dado joint was tight enough that screws were no longer required for the remaining staves. I periodically checked the staves to make sure they were vertical.
Last, but not least, as I was assembling the tub, I lost faith. (Correctly so, as it turned out.) Did the quality of my milling result in a tight enough fit between staves so the water-swelled staves would hold the water in the tub? Maybe not. So, I laid a bead of silicone caulk in each cove cut before placing each stave. It was a “belt-and-suspenders” bit of project insurance. Only my pride was damaged.
The completed tub assembly is pictured below. After months of fiddling with this project, it seemed as though a long, hot soak in my new cedar hot tub was on the horizon. A picture not taken would have shown the use of two sets of cheap ratchet tie-down straps (commonly used to secure loads in trucks and trailers) to keep the staves really tight while the wire rope clamps were cut to size, assembled and installed. If you don’t use the tie-down straps, you will find you lack the slack in the turnbuckle to sufficiently tighten the clamping assembly.
Not pictured in detail (but visible as the dark stave at the back of the tub) was an adjusted filler piece for the final stave. Notwithstanding the use of a CAD tool to design the staves and tub bottom, my milling was off enough that that I was about ¾” short of filling the circle with my standard staves. I used one of the extra staves and a little bit of milling (grooves and a spline) to create a single oversized stave from two staves.
Spa Pack Box
I needed a weatherproof cover for my spa pack, since it would be exposed to the elements. In keeping with the cedar theme, I used 1×6 T&G cedar to construct a box. The inside seams of the box cover boards were sealed with a bead of silicone caulk after assembly. I wanted to be safe, even though the tongue-and-groove joint might have been sufficient to keep the electrical equipment dry.
The completed box with cover is shown above. Note the 1” ventilation holes on two sides covered with brass screening on the inside to help cool the unit. It may be a bit of overkill, since spa packs are typically placed in small enclosures. But it was a simple fix to avoid any overheating issues. I also added a 1×6 T&G removable cedar screen to hide the plumbing to the tub jets and the suction unit. A similar screen was built on the opposite side of the tub.
Wiring the Spa
All spas must have a separate spa panel located no less than five feet from the tub. I used a 50-amp unit purchased on Amazon with a GFCI circuit breaker. I wired it myself from the pre-wire that was installed when I built the house. If you don’t feel comfortable with electrical work, call an electrician. This is extremely dangerous if not done properly and a mistake could also fry the controller on your spa pack.
If you don’t have power to your hot tub location, you will also need to run a dedicated circuit from your panel. And a final caveat, even if you plan on using 110 power for your spa pack, please don’t use an extension cord from an outdoor outlet. The spa pack must be hard-wired to a separate panel.
Plumbing
I used flexible 1-1/2” PVC pipe to run from the outlet of the spa pack to the two jets as well as from the suction to the intake of the pack through the filter. The tub itself is isolated from the spa pack and filter holder using two gate valves. This allows changing the filter without draining the tub. Where possible, the flex pipe was wrapped in double reflective insulation (Reflectix) to reduce heat loss during filtration and heating cycles when the pump is running.
I should note that our hot tub was meant for quiet soaking rather than as a massage spa with lots of noisy jets. Nor does the spa pack include an air blower for air jets. In addition to the noise level, air jets mean more penetrations into the tub and more plumbing that could leak.
Our two jets and suction intake are used only for circulation to heat and filter tub water. Finally, finding spa parts that could work with 2x lumber took a bit of research. I bought the jets and suction intake from a small outfit in central New York. My advice is: order the long or extended version of these units.
Spa Tub Bench
I have no pictures of the bench that sits inside the tub. It was constructed from 2×6″ cedar boards in a hexagonal shape. It is screwed to the floor of the tub.
Cover and Step Stool
Also staying with the natural cedar look, I decided to build my own cover from 1×6″ T&G cedar boards (one-inch foam insulation underneath) and a step stool using 2×6″ cedar boards. The cover looks good, but it proved to be very unwieldy for one person to remove.
Build a Cedar Hot Tub: Fill It with Water!
As the preceding image shows, it looked like we were done and ready to fill the tub. I hooked up a hose and turned on the water. I expected a few leaks as the tub filled and absorbed water. Indeed, I assumed it might take a couple days before the leaks stopped.
The tub did leak. And leak. And leak. True, the rate of leaking slowed over a couple days, but it never got below losing 15-20 gallons a day. Worse, it was almost impossible to determine the location of the leak.
Another issue that become apparent within a day was the tannin leeching from the cedar. It was unlikely to be toxic. (In fact, it was much like swimming in a lake with wind-fallen trees.) But sitting in a bath of dark cedar “tea” just wasn’t appealing. Draining and filling the pool several times might have eliminated most of the leeching. But I wasn’t certain.
The straw that broke the camel’s back was trying to manhandle the cedar cover. It was a two-person job to remove it, and that restricted us from using the hot tub.
Bottom line: a leaky hot tub filled with a dark tea and an unwieldy cover wasn’t what I had planned to build. In my darkest moments after reaching this conclusion, I envisioned a large bonfire of very expensive, milled cedar boards.
Post-Mortem Analysis of the Build a Cedar Hot Tub Project
I decided against the drama of a hot tub pyre. Instead, I tried to first understand why my construction had failed and then to investigate remedies. The hot tub cover can be attributed to a bad design. Even as light as cedar is, a five-foot diameter cover of 1×6″ cedar still weighs a lot, and it is very cumbersome to move. A hinged cover might have been an improvement, but still not ideal. Plus, the overall insulation value was too low. It had to go.
After considerable pondering, I concluded that my multi-pass joinery using house-framing-quality, low-power tools wasn’t up to the task. Milling the joints required a serious, high-powered joiner with a professional automated feeder that could precisely cut the cove and beads in a single pass. Each time I ran a stave through my table router setup, I was no doubt off a bit. Even 1/32nd of an inch error compounded over many passes created stave joints that simply didn’t fit well.
I did try one attempt at draining the tub, letting it dry and then applying a small bead of silicone caulk at each joint. After refilling, the leak rate was lower but still appreciable. And that effort did nothing to mitigate the “cedar tea” issue. I explored various techniques for lining the tub. A heavy, silicone roof coating might work. So would gluing on some sort of vinyl material.
The Solution
In the final analysis, I decided we wanted a functional, attractive and energy-efficient hot tub that we would enjoy using. I found a hot tub vendor in Canada who makes hot tub liners for his products. He agreed to would make a custom liner for my tub. It was expensive ($600 with all the trimmings), but it was well made and performed as advertised. I probably could have sourced the vinyl myself, but the thought of cutting and gluing large pieces of vinyl on the garage floor wasn’t appealing. The vendor in Canada also supplied a vinyl coping for the top of the tub to minimize the risk of wearing, as well as strip glued to the top edge of the liner to hold the clamping strip.
Another $425 for a custom cover from Spa Depot and we were good to go (almost). I discovered even a vinyl-covered, folding cover with a foam core was still too cumbersome for single-handed use, so I made a simple storage rack that permitted me to easily slide the folded cover on and off the rack with minimal effort.
Build a Cedar Hot Tub: The Finished Project
With the solutions discussed above, we finally have an enjoyable hot tub that looks good, is easy to maintain and is a delight to use. With the insulated cover and reflective, double-layer insulation I installed between the vinyl liner and the wooden tub, the heating costs are manageable and well worth the benefit we receive from our relaxing soaks.
Just for Fun:
Click here to see What’s Trending on Amazon.com
Also, read Gas vs. Electric Power Equipment before you buy any new power tools.
Lessons Learned
Every project can be a learning exercise and this one was no exception. My cedar hot tub project turned out to be more complex than I expected. It also took far more time than planned. In the end, I’m glad I did it, but I probably wouldn’t do it again.
A few recommendations for those who want to undertake the How to Build a Cedar Hot Tub project:
- If you just want to soak in a hot tub and don’t care too much about the aesthetics, just buy a basic plastic spa. A fully equipped basic unit can be found for under $3,000. That’s somewhat less than the cost of my cedar hot tub after the liner and cover were purchased. And a used spa in good condition is one-third to one-half that cost. Honestly, this is what I would do the next time I need to install a hot tub.
- If you really want a cedar tub, explore the many kit choices on the market. They are not cheap, but the aesthetics add value, especially with the clear cedar they use.
- If you still want a cedar hot tub on the cheap (around $3,000-3,500) and want to attempt this build, start with the assumption you will need a vinyl liner and insulated cover. This immediately makes your joinery an order of magnitude simpler. All you need are the two passes for bevel cuts on each stave as well as the dado notches to fit the staves around the tub bottom. The bottom boards don’t even need to be trimmed, just cut to length.
Some tips for others: I used cheap pine and a bead of silicone sealant between each joint and it was water proof from the start. For ease of cleaning I eventually made a liner from PVC cloth (like the kind used on inflatable ribs). This stops the leaching too. Also, to save on costs when not used often, I just fill the tub from the house hot water system and keep it warm for the day with a cheap spa heater.
Chris – did you use the silicone “in the joint” and what are “inflatable ribs?”
Good writeup, especially the lessons learned…thanks!
I just want to say thank you for being honest about the difficulty in getting this done.
Thank you for sharing your cedar hot tub project with those of us who want to build our own hot tub and keep the cost down. Especially thank you for doing the step by step. And explaining what did and didn’t work out.
I appreciate your truthful sharing about how hard this project was, and I admire your persistence and the completed lovely project. My husband always has to curb my, “We can do this mentality”. He’s like, “No, I’m tired I don’t have enough tools.” Then I sometimes try it anyway and hurt myself.
Lately I got the idea to order a blow-up hot tub to put on our back porch. It was cost effective, and I’m excited and awaiting the delivery for my birthday. It’s not cedar like my dream tub, but we will see wish me luck!
Enjoy your amazing cedar tub! You are a Rockstar of tub builders. Stay well. 🌴🙏🕊️😃
Hi! Thanks for the amazing write-up. I have inherited a cedar hot tub that has been out on the elements and needs refinishing. How should I go about this? Do I need to use a stain or sealer on the wood?
Thank you!
Paige
Hi Paige–
Gary Ebersole says the interior finish on the wood should definitely be left natural. If it’s a professionally manufactured tub that did not leak when it was previously filled, the wood needs to absorb water to expand and seal the joints. A sealer on the inside of the tub would prevent that.
In terms of stain, Gary says he would personally not add any chemicals that might be in contact with whatever sanitizing solution you plan to use. The interior surfaces can be sanded without any issues. The exterior can be stained or finished however you prefer.
I’m currently in the process of restoring a 1980’s California Cooperage 6′ diameter X 4′ deep tub made all of CVG magogany. It’s been in dry storage for decades, and I did replace two of the floor boards towards one end (of for areas of dry rot, on for bad cupping). Other than that, plan to use all original pieces. If I cannot get it to hold water, I will just go the route of the liner as you did. Although, I’ve read that Firestone EPDM pond liner is a good product for such lining since it has 30 year life and chemical resistant. Of course, this will require the cutting and gluing you (understandably) avoided with the pro-made liner. I can get an all one piece 15×15 epdm sheet for about $350. So may go that route. I was thinking similar on the cover, but after reading your journey, will instead make a cedar “roll up” cover much like the Great Norther co makes and sells. Will use flexible and UV stable poly foam board at 1/4″ thick and cut trapezoid boards at the profile shown on many website examples. Interesting to note, Ca Cooperage offered same type of roll cover back in the 70’s…reportedly the first to do so. I have the original order form, installation manual, maintenance book, etc., that came with the tub. Got everything for $300! Quite the bargain if it holds water…and even if it doesn’t I think. All staves have tongue and groove sides, that are also cut at a bevel. AND, all staves are also cut as curved on inside and outside faces. Not sure what type of tools one would even need to create these pieces. I imagine a special planer that cuts the initial 2″ material into the curved shape. Every tub size would need slightly different curve, bevels, etc. They offered 4 sizes, 4′, 5′, 6′, and 7′. Needless to say, they fit together quite nicely with these profiles…and quite the craftmanship! If I made a tub, I’d probably go for Alaskan yellow cedar, and canoe joint as you did. We had a 4′ Alaskan yellow tub, and loved it, although a bit tight for more than 2 people. Anyway, probably more info that you are interested in, but wanted to say thanks for taking the time to do your write up…it gave me some good insight and ideas! Also, I hope your “compound” is going together well. Sounds like quite the spread you are creating for yourself. We are in the midst of a full restoration of a river frontage house that one could have easily deemed “ready for bulldozing”. We are going to the studs on most of it, and about 80% done. It is so much hard work, and doing most of it ourselves…but also so incredibly rewarding. My wife and I are in our mid 50’s, but I would recommend this kind of adventure to anybody able bodied. It’s a once in a life time thing for us, but no regrets at all. Every day there’s plenty to do, and every day is different. What else could one ask for? Good luck and thanks!
Doug
When you get to the staves, you could use a trick from old wood boats. If you shop around you can find cotton caulking you twist it and pound it in so you tighten the twist. Unlike commercial caulking cotton can get dry and wet when the wood swells it just squeezes and seals.
Avoid vinyl liners. It is extremely difficult to get any glue, even vinyl glue, to stick. Plus, even extra heavy duty vinyl will wear out pretty fast. I like the pond liner idea.